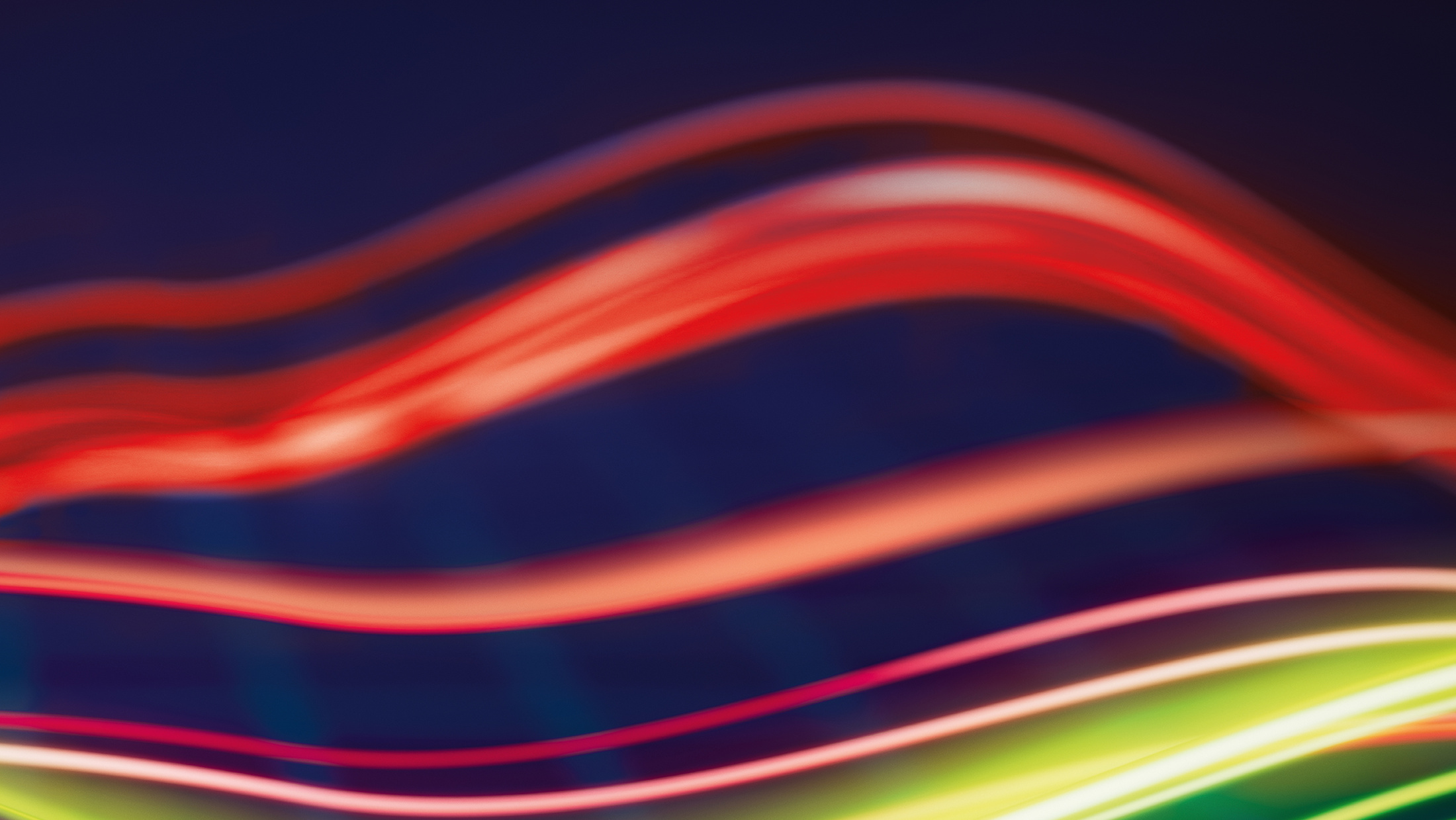
Automation at KRONE
Automation. A word with many possibilities. At KRONE, too, this focus has several manifestations. These include the modern and partially automated production steps at the production sites such as Herzlake, but also automated products such as the Box Liner Automatic. Let us show you how we produce our products and what our innovative trailer solutions look like.
Have you ever taken a tour of our plant in Herzlake? Then find out here how our products are produced automatically there.
Automated floor frame production
Only a few human hands are needed to feed the parts for the side rails to the welding robots in the globally unique automated floor frame production. A total of 18 robots produce 25 metres of clean MAG weld seams with 550 spot welds in less than 15 minutes. The finished floor frame then goes to the blasting system for quality control and then to the cathodic dip-paint bath.
Augmented Reality
During this safety check, digital elements are inserted into a real image. In this way, the entire vehicle can be compared with a target data set, currently via a tablet - KRONE thus guarantees the completeness and positional accuracy of the components. Augmented reality therefore shows where a component may be missing or even the wrong component has been installed.
However, there are a number of products where millimetre accuracy is also important. In Herzlake, for example, every automatically produced floor frame for KRONE swap bodies is measured to an accuracy of half a millimetre in a light-proof measuring booth.
Automation of the KRONE Group
We are committed to state-of-the-art production facilities in all KRONE factories in order to be able to guarantee consistently high product quality.
Silver Robotics is the former equipment manufacturing company from Herzlake. Today, Silver Robotics is a separate company for the planning and realisation of automated systems with additional services.
The KRONE Group has automated many logistics processes. For example, UPCs (Under Pallet Carriers) are used at the interfaces between high-bay racking, storage and the picking stations.
Advantages of UPCs:
- Space saving: UPCs move under the pallets and do not require any additional space for forks or lifting devices. As a result, storage density can be increased and the available space utilised more efficiently.
- Speed and efficiency: The UPCs can pick up, transport and set down pallets very quickly. This reduces throughput times in the warehouse and increases the efficiency of the entire system.
- Flexibility: They are able to work in different racking systems and on different warehouse floors, making them suitable for different warehouse layouts and types.
- Reduced infrastructure costs: As UPCs operate autonomously and do not require complex infrastructure such as rails or conveyor belts, warehouse infrastructure costs can be reduced.
- Energy efficiency: UPCs are typically lighter and require less energy than traditional automated conveyors, resulting in lower operating costs and a more environmentally friendly storage solution.
AutoStore is an automated storage system in which small robots travel on a compact grid above stacked bins, lifting them as required for picking and transporting them to the picking stations. Thanks to this innovative technology, AutoStore maximises space utilisation and significantly increases efficiency in modern warehouses and logistics centres.
Advantages of AutoStores:
- Goods-to-man principle with 16 robots.
- Maximum scalability thanks to modular system.
- Easy to expand by extending the grid.
- Capacitive scalability by adding robots.
- High storage density by stacking the containers.
- Extremely low power consumption with maximum efficiency.
- Energy recovery of the robots when lowering containers.
The silo-style automated pallet warehouse uses the full height of your building to store pallets efficiently and make them accessible at lightning speed, maximising your storage capacity and minimising space requirements. With high storage density and fast flow of goods, this system offers a future-proof solution for your logistics requirements.
Advantages:
- Goods-to-man principle with 3 storage and retrieval machines.
- Maximum space utilisation: Full use of the building height thanks to integrated warehouse and building design.
- High efficiency: Fast access to pallets thanks to automated storage and retrieval machines.
- Reduced operating costs: Energy-efficient operation and less manual labour.
- High process reliability and speed.
- Maximum availability and efficiency.